Shibori in the Shape Making Strategy
Jun Nakamura
Shibori in the Shape Making Strategy
Jun Nakamura
Japan / UK
As people live closer to technology and purchase mass produced goods, the demand for handmade products has decreased and many traditional handicrafts are in danger of extinction. The Japanese traditional craft of Shibori has been struggling to pass on its rich heritage to new generations. Shibori was developed originally for Kimono and is commonly associated with tie-dyed effects - for this reason, plain coloured fabric has been preferred. In contrast, JU-NNA processes Shibori innovatively by using printed fabrics.
JU-NNA’s practise of Shibori began with the idea of shaping garments without using darts. Through experimentation the focus shifted to the 3D surface - originally a by-product and a unique quality that Shibori gives to fabric. Inspired by abstract arts, JU-NNA started to test these techniques on printed fabrics, which has led JU-NNA to pioneer the processing of Shibori on prints.
To process Shibori, artisans bind a fabric by making individual knots with thread by hand, and then use steam to make the fabric retain its shape. After removing the thread, the tiny 3D shapes of Shibori remain on the fabric, which makes the fabric very stretchy and flexible. Many challenges had to be overcome in this project: the Shibori structure itself makes the design process very complex for a number of reasons. Firstly, the width of fabric is reduced by up to half, which varies depending on the type, the size, and the density of Shibori. Therefore, prints need to be created that take shrinkage into consideration, because prints look very different after processing with Shibori. Secondly, there are limitations to the weight that the Shibori components can support - this makes structuring garments very complex. Shibori fabric is unable to support a heavy weight, therefore it cannot be used for upper parts of garments - for example around the shoulders - because that makes Shibori stretch out and lose its 3D structure, unless a base structure is underneath to support it. In addition, Shibori patterns have to be placed carefully in relation to seamlines, in order to achieve a clean finish. Seam allowances on Shibori may become too thick, which gives another limitation on the garment structure. The process of marking out Shibori on printed fabrics is more difficult for artisans to see and therefore requires them to bind the fabric by eye, putting restrictions on potential patterns. Other issues include available fabric quality, fibre composition and the length.
Problem solving through creative practice has enabled solutions to be found and led to a really new approach to Shibori. It has taken JU-NNA years to discover the best balance for his designs, yet there are still more ways to be explored. Through this innovative practice, many colours and prints are combined within the unique Shibori structure of JU-NNA’s garments, which JU-NNA hopes will support the preservation of this precious, heritage craft.
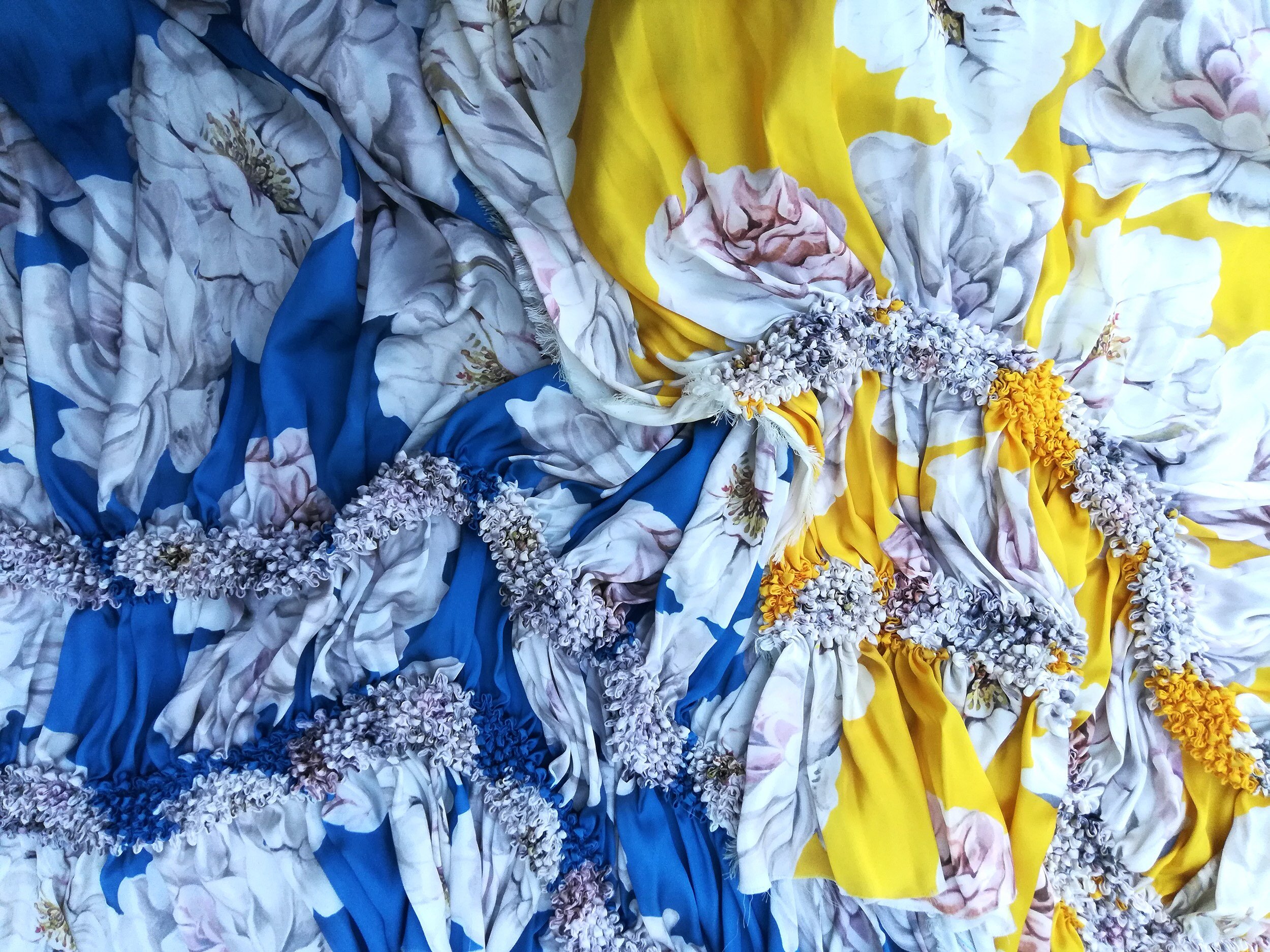
Signature style Shibori on surrealistic flower prints. Shibori in the Shape Making Strategy. JUN NAKAMURA.
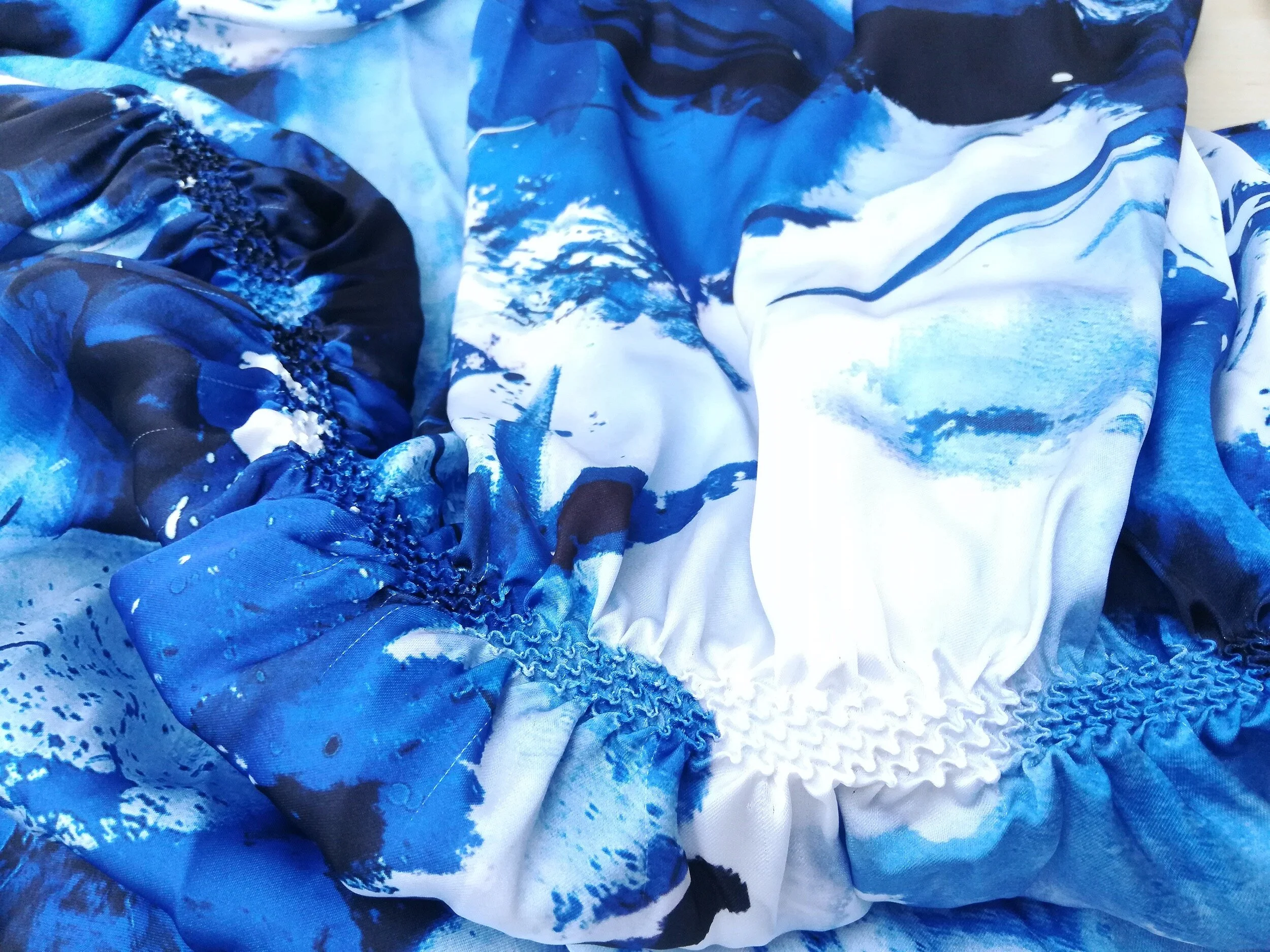
Delicate style Shibori on a blue abstract art print (Collaboration with Anke Ryba). Shibori in the Shape Making Strategy. JUN NAKAMURA.
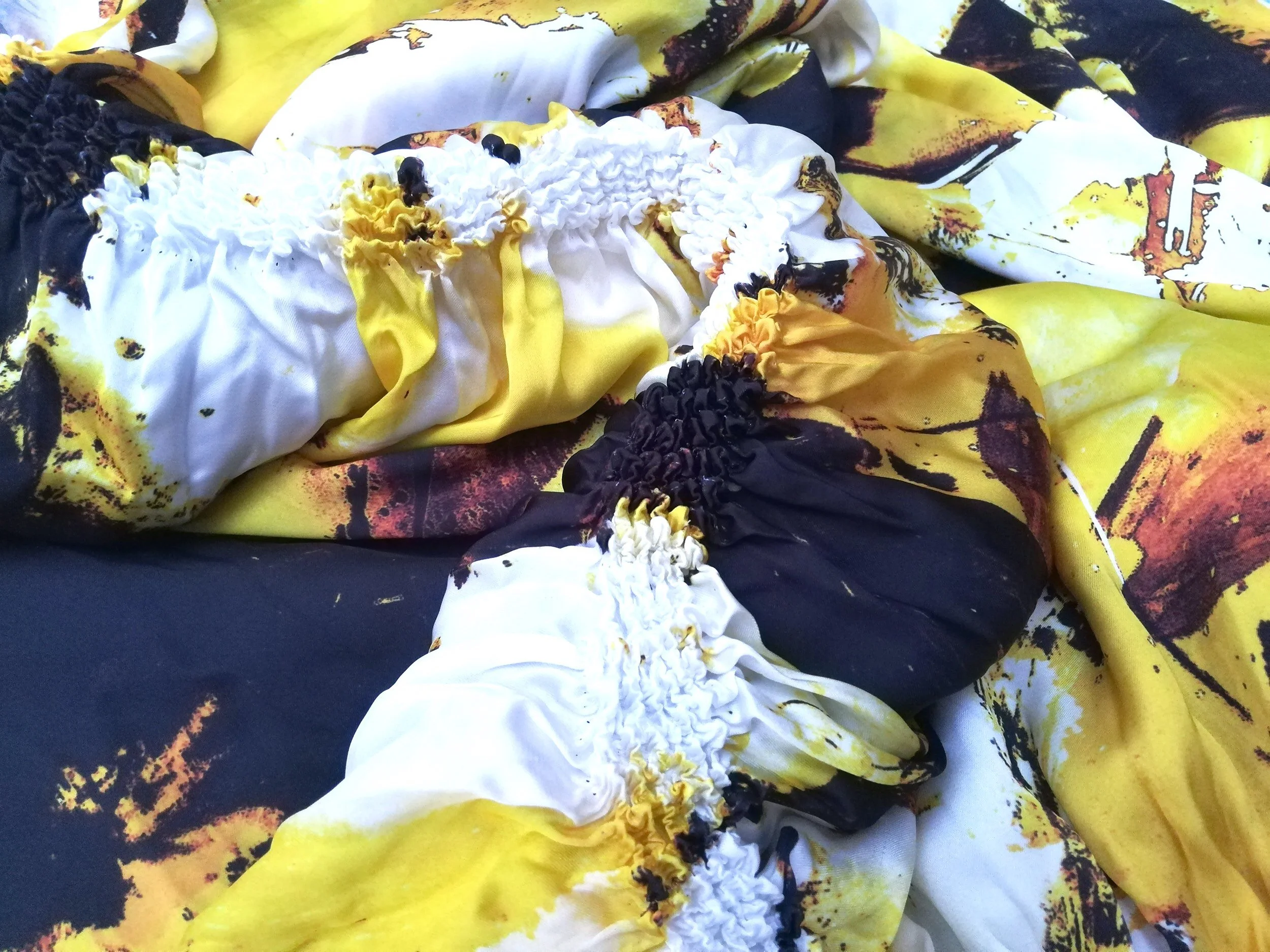
Signature style Shibori on a yellow abstract art print (Collaboration with Anke Ryba). Shibori in the Shape Making Strategy. JUN NAKAMURA.
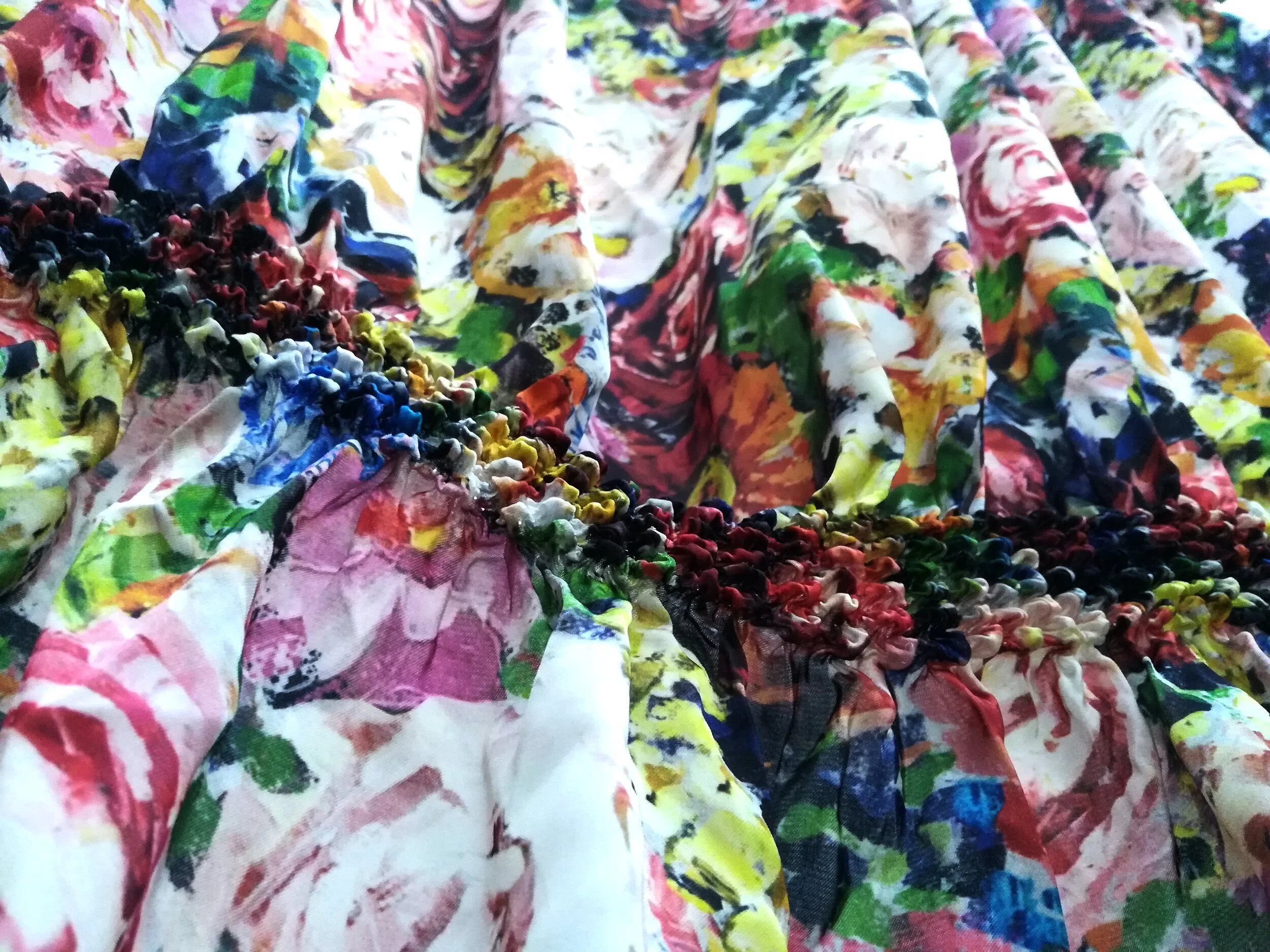
Signature style Shibori on an oil painting flower print. Shibori in the Shape Making Strategy. JUN NAKAMURA.

Signature style Shibori on a black satin. Shibori in the Shape Making Strategy. JUN NAKAMURA.

Shibori trial for SS21 collection. Shibori in the Shape Making Strategy. JUN NAKAMURA.
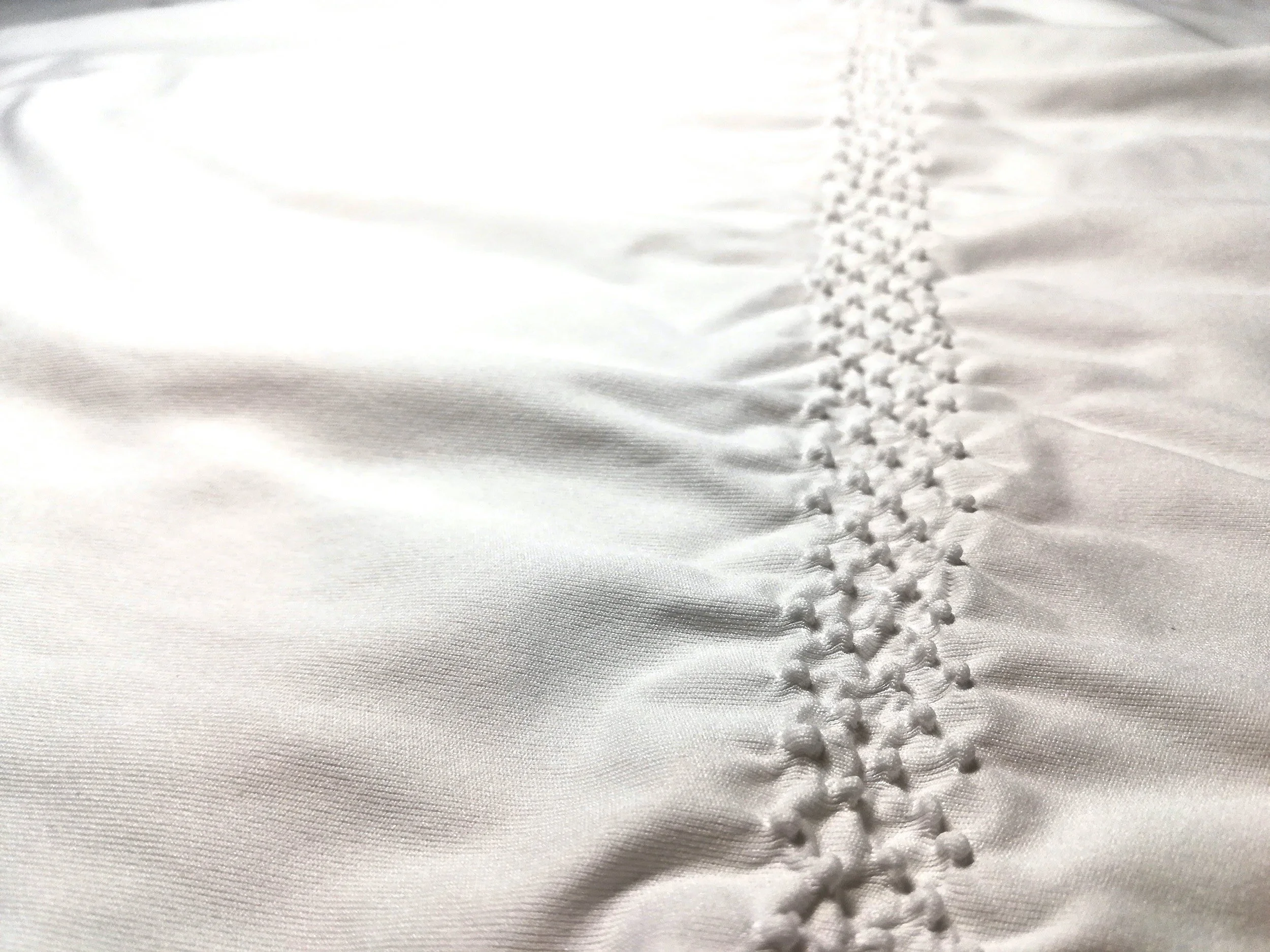
Delicate style Shibori on a jersey. Shibori in the Shape Making Strategy. JUN NAKAMURA.

Shibori on a logo print. Shibori in the Shape Making Strategy. JUN NAKAMURA.
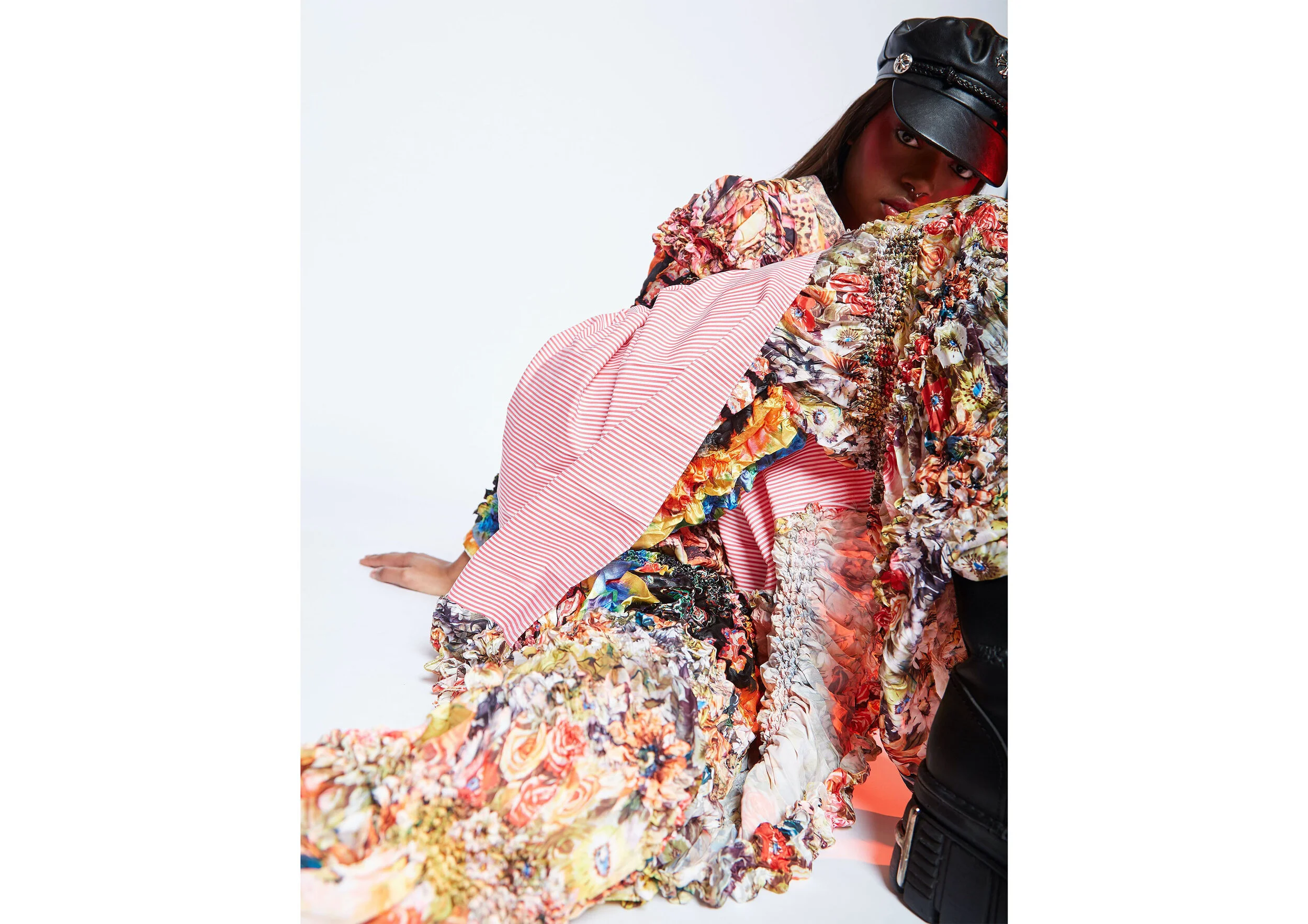
First collection. Shibori in the Shape Making Strategy. JUN NAKAMURA.
Bio: Jun Nakamura
website: https://www.ju-nna.com
email: info@ju-nna.com
instagram: https://www.instagram.com/ju_nna_
facebook: https://www.facebook.com/junnashibori/
Jun is a founder of JU-NNA. He studied MA Fashion Design Womenswear at Istituto Marangoni London after working in the Japanese fashion industry. Jun’s first collection was nominated for both Mittelmoda The Fashion Award and Fashion Scout Merit Award in 2018 while he was in the university and his collection was featured in many magazines and articles. Following the completion of his study, Jun was granted an Exceptional Talent Promise visa with an endorsement from the British Fashion Council and he started JU-NNA in 2019.